
いま、中小企業の人手不足が深刻化している。日本商工会議所が今年7月から8月にかけて行った調査によると、「人手不足」と回答した企業は68%で、2015年の調査開始以降、最悪の結果となった。だが、中小企業が、人手不足だからといって安易に人員を増員させることには思わぬ危険性がある、と、自身も社員数50名の新聞販売店を23年間経営した経験を持ち、多くの企業の経営支援に携わる米澤晋也氏は話す。本稿では、米澤氏が、人手不足の中小企業が増員前にすべきことについて、具体的な事例を交えて解説する。
中小企業が「すべきことをせずに増員する」ことの危険性
中小企業の人手不足が深刻化しています。日本商工会議所が今年(2023年)7月から8月にかけて行った調査によると、「人手不足」と回答した企業は68%に上り、2015年の調査開始以降、最悪の結果となりました。
東京商工リサーチの調査では、コロナ禍で人員削減をした企業の61.5%が、人材の補充回復ができずにいることが分かりました。
人手不足のしわ寄せは、現場スタッフに。現場からは、「人を増やして欲しい」という切実な声が上がっていることと思います。しかし、増員する前に、すべきことがあります。それをせずに増員しても、余計に忙しくなったり、労働生産性が下がる危険性があるのです。
すべきことを正しく行うことで、少数精鋭の組織になり、最終的には、賃上げの可能性もあります。本記事では、増員の正しい実務について解説します。
人を増やしたら、やる事も増えた……とならないために
人員を増やしたら、余計に忙しくなったというケースは、教育システムがしっかりしていない企業でよく起こります。教育システムがないと、いつまで経っても部下は仕事を覚えず、何度も上司や先輩に「これで良いですか?」と確認することになります。上司や先輩は、そのたびに自分の仕事の手を止めなければならず、仕事が滞ります。教育システムがしっかりしていないとミスも頻発します。
ミスがあると、周りのスタッフもリカバリーに多くの時間を奪われます。ミスが頻発すればチェック機能を設けなければならず、手間は増えるばかりです。気が気でなく、休日出勤することが増えたという上司を私は知っています。
チェックやリカバリーに手間を取られると、仕事が遅れます。遅れは次工程に引き継がれ、蓄積し、組織全体の生産性が悪化します。
教える側、教わる側、双方にストレスがかかり、人間関係が悪化し、せっかく育てた新入社員が数ヵ月で辞めてしまうということにもなりかねません。こうした悲劇を防ぐために、採用前に教育の仕組みを構築することが大切です。
人員を補充する前に、効果がない仕事を廃止する
増員する前には、業務効率の改善も欠かせません。効率の悪い状態で増員すると、労働生産性は著しく低下します。業務効率改善のためには、次の2つに取り組む必要があります。
1.効果のない仕事の廃止
2.滞りの改善
最初に、効果のない仕事を浮き彫りにし廃止します。「ウチは、そんな無駄な仕事はしていない」と言う方がいますが、洗い出してみると、想像以上に多くあるものです。
効果のない仕事が生まれるのは「人間の真面目さ」が原因です。私たちは、社会人になりたての頃、先輩や上司から、「仕事が終わったら、自ら次の仕事を見つけなさい」と指導されてきました。何もせずにいると罪悪感を感じ、新たな仕事を作り出してしまいますが、そこで作られた仕事のほとんどは、大した効果のないものばかりです。
とある小売店では、活用もしない顧客カルテを作ったり、必要以上に綺麗な出勤表を作り出すスタッフが現れました。さらに、スタッフがちゃんと仕事を作り出しているかを管理するために、報告書を書かせるなどという付帯業務まで増えたのです。
効果のない仕事は、勤務時間を満たすまで作られます。中には、連綿と後輩たちに受け継がれていくものもあります。
人員を補充する前に、効果がない仕事を廃止しましょう。効果のない仕事の判別法は簡単です。「この仕事は何を生み出していますか?」という問いに即答できない仕事が廃止の候補です。候補が出たら、試しにやめてみます。やめて問題があれば復活すれば良いのです。やってみると、想像以上に廃止できると思います。
仕事の滞りをなくし、半年間で1,000万円以上の生産性向上を実現した菓子店
仕事が忙しくなると、労働時間や人員を増やすことを考えてしまいますが、「減らす」ことに目を向けることが大切です。減らすものとは非常にシンプルで、前述の効果のない業務と、今から説明する「滞り」です。
滞りを減らす実務を、菓子店をモデルに説明します。ある菓子店では、次のような工程で菓子を作り販売しているとします。
「原材料の仕入れ」(10)→「製造」(5)→「ラッピング」(8)→「販売」(11)
括弧内の数字は、それぞれの工程の、1日あたりの能力です(仕入れは1日あたり10個分の菓子の原材料を仕入れる能力がある。製造は5個の製造能力、ラッピングは8個、販売は11個)。
このモデルでは5個しか顧客に届けることができません。一番弱いラッピング工程(ボトルネック)が全体の能力を決めるからです。実際の職場も、工程によって能力のバラツキがあり、ボトルネックがあるはずです。
ボトルネック工程(製造)で仕事が滞り、スタッフは忙しくしています。ボトルネックの次工程(ラッピング)では、仕事が流れてこないので「待ち時間」が発生します。この待ち時間が生産性を下げる要因です。
実際の菓子店の事例を紹介します。その菓子店でも製造がボトルネックでした。対策として、最初に効果のない仕事を廃止しました。
次に、お菓子づくりに集中するために、お菓子づくり以外に費やしている動作や作業を洗い出しました。すると、保管庫が別の階にあるため、原材料を保管庫に取りに行くという動作に結構な時間を費やしていることが判明しました。
そこで、仕入れスタッフが運搬を代行しました。さらに、掃除など他の工程のスタッフにもできる作業を分担しました。その結果、業務時間が大幅に減り、半年間で1,000万円以上の生産性向上を実現したのです。
先程のモデルで表せば、次のように改善されたのです。
「原材料の仕入れ」(8)→「製造」(8)→「ラッピング」(8)→「販売」(10)

改善前も後も、全体の能力の総和は変わりませんが、協力し合い滞りを減らすことで、改善前よりも3個多い、8個をお客様に販売できるようになったのです。このように、人員の補充をしなくても、あるいは最小限の補充で、これまでと同様かそれ以上の生産性が実現するのです。
実際の現場では、製造する商品が変わったり、スタッフが休んだりといった様々な要因により、ボトルネックが他の工程に移動します。絶えずチェックと改善が求められます。
労働生産性が高まれば、限られた人員で利益を生み出すので、賃上げの可能性も期待できます。
本記事で解説した手法は、時間やコストをかけずに実行できますので、人員を増やす前に、考えてみてはいかがでしょうか。
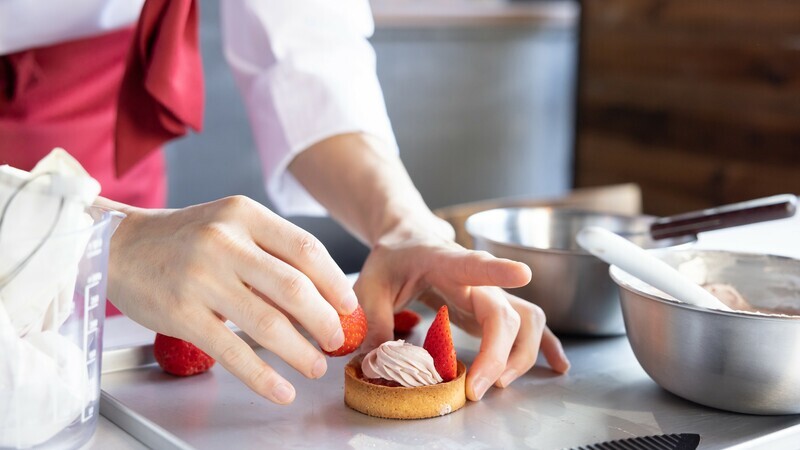
コメント