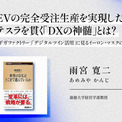
今、世界中の企業が取り組むDX。日本でも、新旧を問わず、多くの企業がDXと向き合うが、技術の導入や業務改善どまりのことも少なくない。産業、業種の垣根を超え、DXでビジネスモデルや組織全体を変革するカギはどこにあるのか。当連載は、国内外のDXの先進事例が多数収録された『世界のDXはどこまで進んでいるか』(雨宮 寛二著/新潮社)より、一部を抜粋・再編集。2030年代を見据えた「DX変革」の最前線をお届けする。
第2回目は、アメリカの電気自動車大手テスラのCEOイーロン・マスクが推し進めるDXの、先進性と独創性をひも解く。
<連載ラインアップ>
■第1回 GAFAM、ウーバー、ネットフリックス、ユニクロが実現するデジタル変革とは?
■第2回 EVの完全受注生産を実現したテスラを貫く「DXの神髄」とは?(本稿)
■第3回 AIと最先端テクノロジーでタクシー市場を変革したウーバーの革新性
■第4回 IoTとAIをフル活用、店舗を急速アップデートするウォルマートのデジタル変革
<著者フォロー機能のご案内>
●無料会員に登録すれば、本記事の下部にある著者プロフィール欄から著者をフォローできます。
●フォローした著者の記事は、マイページから簡単に確認できるようになります。
●会員登録(無料)はこちらから
2.テスラ:自動運転を見据えたDX
現在、電気自動車(EV:Electric Vehicle)の開発は、自動車業界においてニューノーマルとなりつつありますが、EVの存在をグローバルレベルで知らしめたのは、他でもないテスラです。
テスラが創業時に掲げた会社としてのコンセプトは、既存の自動車メーカーとは異なるものでした。自社のあるべき姿を「テクノロジー企業の側面を持つ自動車製造企業」とし、そのコアとなるのは、「バッテリー、ソフトウェア、独自のモーター」であるとしたのです。
この考え方は、従来の自動車メーカーが、自動車づくりの根幹に置くエンジンありきの発想を覆すものでした。イーロン・マスク氏は、2006年にテスラ最初の電気自動車となる「テスラ・ロードスター」のコンセプトを発表した際に、「炭化水素経済から太陽電池経済への移行を促進する」ためにテスラは存在すると述べましたが、この存在意義は、創業時に掲げたあるべき姿をより具現化するものとなりました。
実際にテスラ・ロードスターが販売開始となったのは2008年ですが、この時期の自動車業界は、トヨタのプリウスに見られるようにハイブリッド車中心の開発に留まるものでした。伝統的な自動車メーカーが、まだエンジンを主軸に考えた発想で自動車開発を進める時代に、既存のコンテクスト(文脈)に囚われず、異なる次元で発想してロードスターを完成させたところにテスラの革新性を読み取ることができます。
既存のコンテクストに縛られないとの発想は、独創的な販売形態や製造プロセスにも見て取れます。テスラは、伝統的な自動車メーカーとは異なり、「完全受注生産型」の形態を採っています。それを支えているのが、自社完結型の製造プロセスです。一般的に、自動車1台を組み立てるのに約3万個の部品が必要とされることから、自動車の組み立てには、各部品を製造するメーカーが多数存在します。日本では、これらの部品を自社で内製している率(部品内製率)が30%に留まり、70%は部品メーカーであるサプライヤーに依存しています。
日本の自動車メーカーが部品の供給の多くをサプライヤーに依存するのは、部品の開発や生産をアウトソーシングすることで、自動車メーカー自身の開発や生産に関わる業務量を節約し開発時間を短縮することが可能になるからです。
他方、米国では部品内製率が70%に達しており、日本とは対極的な状況にありますが、テスラは、これよりもさらに垂直統合度が進んでいます。座席からバッテリーセルに至るまでほぼ全ての部品が内製でまかなわれています。自前で多くのハードウェアを設計しソフトウェアを作成しているため、他の自動車メーカーが望めないほどの水準で車の製造プロセスをコントロールして完成度を高めることができるのです。
たとえば、2020年以降のコロナ禍で半導体の供給が困難に陥った際には、部品内製率の高さから、製造プロセスにおける臨機応変な軌道修正が可能となりました。テスラは自社で基板を設計しているため、パワーチップなど代替品を受け入れる形に即座に設計変更が可能であったことから、他の自動車メーカーにとって打撃が大きかったサプライチェーンの混乱をめぐる問題にもうまく対処することができたのです。
これに対して、日本の自動車メーカーや米国の一部の自動車メーカーは部品内製率が低いことから、リスクを伴う半導体の修正や、別の半導体工場の製品を使うことには慎重にならざるを得ませんでした。そのため、その対応には多くの時間が費やされることになったのです。
このように、テスラは、垂直統合度を高めた独自の製造プロセスを構築することにより、分業や組み立てコストを圧縮し、コストダウンを目的とした大量生産を図ることや余剰在庫を売り切る必要性を排除することで、「完全受注生産型」の自動車メーカーを貫いているのです。
ギガファクトリーとデジタルツイン
テスラの生産拠点は、「ギガファクトリー」と呼ばれるスマートファクトリーです。この名称はマスク氏の造語ですが、それは文字通り10億を表す単位のギガに由来し、リチウムイオン電池などのバッテリー(蓄電池)の効率的な生産に視点が置かれています。
なぜなら、電気自動車は価格の3~4割をリチウムイオン電池が占めることから、電気自動車のコストを下げるには、バッテリーの製造コストを削減し低価格化を図ることが最優先になるからです。ギガファクトリーの中でも米国カリフォルニア州にあるフレモント工場は、北米で最も生産性の高い自動車工場として知られています。ギガファクトリーを見れば、テスラが電気自動車を作る自動車企業ではなく、テクノロジー企業であることが理解できます。
マスク氏による工場の捉え方は、極めて独創的です。その捉え方は、「工場をプロダクト(製品)であると考える」「工場を、マシーンを作るマシーンと考える」などの発言からうかがい知ることができます。つまり、「マシーンという自動車を進化させるより、マシーンを作る工場を進化させた方が10倍も効果が高い」というのがマスク氏の信条なのです。
工場を評価する一般的な指標としては、稼働率や労働分配率、在庫回転率などが考えられますが、ギガファクトリーで重視されるのは、「アウトプット(生産台数)」です。それは、「ボリューム(生産規模)×密度(サプライヤーを含めた生産拠点の稠密〈ちゅうみつ〉性)×速度」という公式で表すことができます。
ここで言う密度とは、ギガファクトリーに太陽光発電やバッテリーなどの生産拠点がどれだけ隣接しているかを意味します。たとえば、ギガファクトリーでは、自動車のアセンブリラインのあるフロアーの上階にリチウムイオン電池の製造スペースを設けて内製化することで、稠密性を高めています。
2021年におけるフレモント工場の製造能力は週平均8550台で、2番手のトヨタジョージタウン工場の週平均8427台に拮抗していますが、1万平方フィート当たりの単位面積で比較すると、トヨタの9台に対しテスラは16台に達しており、その製造能力は1.8倍と歴然の差があることが分かります。
通常、自動車メーカーの工場では、車両がコンベアで運ばれてくるのが一般的ですが、ギガファクトリーでは、車両は無人搬送機に載せられてアセンブリラインを流れてきます。それゆえ、車両に不具合が見つかった際には、コンベアでは製造ライン全体を停止させて事に当たる必要がありますが、ギガファクトリーでは不具合が生じた車両だけを除いて対処すればよいのです。こうした仕組みは、工場の機動性や柔軟性、さらには拡張性などを高めることにつながります。テスラは、生産プロセスにおけるデジタル化や同期化を着実に進めることにより、こうした優れた手法を確立しているのです。
また、テスラ車にはデジタルツインを活用したシステムが標準搭載されていることから、車両のアップデートは全て自動化により行われます。各車両の環境や動作は車両に搭載されたセンサーによりクラウド上へ送信され人工知能がデータを解析します。仮想空間上では、シミュレーションによる性能の微調整やテストなどが常時行われ、気候条件に合わせて車両の設定を最適化するなど性能の向上を確認したうえで、各車両にフィードバックし、自動でソフトウェアがアップデートされる仕組みを構築しています。
こうしたデジタルツインを活用した仕組みが確立されることにより、車両診断をサービスセンターで行う必要がなくなることから、テスラ側では、車両診断にかかるコストを大幅に削減できる一方で、顧客側ではサービスセンターに出向く時間と手間を省くことが可能となるのです。
電気自動車を普及させるための変革
電気自動車は、ガソリンの代わりに電気で走ることから二酸化炭素を排出しないため、環境に優しいという大きな利点があります。この環境保護の視点は、SDGsやESGなど現代の経営の指針となる考え方にも通じることから、更なる導入が期待されています。しかし、その導入には、当初さまざまな課題や障害が存在しました。テスラは電気自動車開発の先駆者として、どのような問題に直面し、それをいかにして克服したのでしょうか。
テスラが直面した最初の問題は、車両価格が高くなることでした。ゼロからの電気自動車開発は、設計、部材調達、製造、マーケティングなどバリューチェーンのほぼ全ての工程が初めての試みになることから、莫大なコストがかかることが予想されました。実際、テスラは、最初の生産車両であるテスラ・ロードスターの価格を9万8000ドル(約1000万円)に設定しています。電気自動車を普及させるには、この価格を下げて庶民の手が届く大衆車としての価格帯を実現することが求められました。
そこでテスラは、製造と販売の両面からコストを圧縮して、価格へのコスト転嫁率を下げることに注力していきます。それは、オートメーション化による製造プロセスの効率化に加え、自社ウェブサイトへのプロモーション活動の一元化やディーラー網による販売コストの削減などです。
こうした打ち手が着実に実を結び、2021年2月に発表されたモデル3の価格改定では、スタンダードレンジプラス(シングルモーター)を429万円、ロングレンジ(デュアルモーター)を499万円に設定して、大幅に価格を下げることに成功したのです。
一方で、電気自動車に電気を充電する施設が少ないことや、チャージに時間がかかることもまた、電気自動車の普及を妨げる大きな問題でした。米国では初号機のロードスターが発売された当時、カリフォルニア周辺にある充電ステーションは僅か数百箇所に留まっていましたが、2019年には、米国における充電ステーションは7.7万箇所まで増加するに至っています。また、充電にかかる時間も当初はフル充電まで8時間程度かかっていましたが、2018年には、高速充電設備「スーパーチャージャー」では、約30分で80%充電完了を達成するに至っています。
このスーパーチャージャーは世界で1.2万箇所に、また、ホテルや駐車場に設置する簡易充電設備の「デスティネーションチャージャー」の設置は1.5万箇所を超えるまでになりました。これらはいずれもテスラ直営の充電ステーションとして今も拡大し続けています。日本でも、人気のホテルやレストラン、リゾート施設などを中心に充電ステーションの開拓が進み、2022年5月までに、デスティネーションチャージャーは2900箇所を超えるまでに拡大しています。
これに加え、航続距離の伸長も進みつつあります。既にフル充電で約500~800㎞の走行が可能になったモデルも存在し、外出先でチャージャーが無くても半径250~400㎞までは遠出が可能となりました。現在ガソリン車は1回の満タン給油で航続距離が平均で600㎞以上であることから、電気自動車の1回当たりの充電は、ガソリン車の航続距離に引けを取らないレベルまでに高まったと言えます。
さらに、電気自動車購入後に必要となるメンテナンス用の施設が少ないことも、購入を妨げる一因でした。テスラはまず、リモートによる遠隔診断により深刻な故障を事前に検知できるようにしました。そのうえで、ソフトウェアによるオンラインアップデートの活用や、技術スタッフであるモバイルテクニシャンを派遣することで、故障車の8割以上をサービスセンターに入庫させずに修理可能にするに至っています。
このように、テスラは、価格、充電、航続距離、メンテナンスなどの問題から生じるさまざまな課題や障害を取り除くことで、電気自動車の普及に努めています。他方で、トヨタやダイムラーなどの競合企業に敢えて電気自動車に関する技術を共有して、電気自動車市場への参入を促す働きも積極的に行って、市場の活性化も図っているのです。
完全自動運転車開発の変革プロセス
電気自動車のパイオニア企業であるテスラが現在取り組んでいるのが、自動運転車の開発です。テスラは、先進運転支援システム(ADAS:Advanced Driver-Assistance Systems)として、「オートパイロット(autopilot)」を自社開発して、完全自動運転化(FSD:Full Self-Driving)に向けた取り組みを進めています。
自動運転のレベルは現在、米国自動車技術者協会(SAE:Society of Automotive Engineers)が設定したレベル0からレベル5までの6つの段階が基準となっています。レベル0は、従来通りドライバーが運転するという状態で、ドライバーが全ての主制御系統の操作を行うレベルを指します。
レベル1からレベル5までは自動運転の程度で分けられており、レベル1は、「自動で止まる」「前方の車に追随して走る」「車線からはみ出さない」など、システムが前後左右のいずれかの車両制御を実施する「運転支援」のレベルで、これを起点にして自動運転の程度が上がっていき、システムが常時全ての運転タスクを実施するという「完全自動運転」のレベルが最高位のレベル5となります。
テスラが目指すレベル5の完全自動運転車の開発は、「ビジョンとプランニングのための高度なAIに基づくアプローチ」によって進められています。AIに基づくアプローチの中心となるのは、「ニューラルネットワーク」と「オートノミーアルゴリズム」の2つで、テスラはこれらの最先端技術を駆使して、「不確定で複雑な現実の状況下で動作する強固なプランニングと意志決定システム(オートパイロット)」を構築しています。
具体的には、車両に取り付けた複数のカメラから映像を取得して、道路レイアウト、静的インフラストラクチャ、3Dオブジェクトなど膨大な生データを解析したうえで、捉えた空間を忠実に再現し、その空間内で車の走行軌跡をプランニングすることで、車を運転するためのコア・アルゴリズムを開発しています。
それでは、このオートパイロットの開発は、現在どのレベルまで進んでいるのでしょうか。オートパイロットは、SAEが設定した基準で言えば、自動運転レベル2を実現する機能まで開発が進んでいます。この機能は、車両に搭載された8台のカメラと車載コンピューター「ハードウェア3」によって実用化されるに至っています。
具体的には、360度の視界と最長250m先の視認が可能な8台の車両カメラにより全方位で取得した情報をハードウェア3が圧倒的な処理能力で理解し、独自開発したニューラルネットを実行することにより、同じ車線内でのハンドル操作や加速、ブレーキを自動的に行うことを可能にしています。
テスラの新型車両には、あらゆる状況における自動運転に対応するために将来必要となるハードウェアが搭載されています。このシステムは、将来的にドライバーによるアクションを一切必要とせずに移動が行えるように設計されていることから、テスラが早期の完全自動運転を目指して開発を進めていることがうかがえます。
テスラは、「ドライバーの監視を必要としない機能を実現するには、何百万マイルにもおよぶ経験で裏打ちされた人間のドライバーを超える信頼性を習得する必要がある」ことを十分に理解して、デジタルツインを活用した開発を進めています。
実際に路上で走行するテスラ車から、車両の性能データや気候データなど膨大なデータをクラウドに集めて人工知能が期待通りに動作するかを診断し、仮想空間で現実の物理世界と同じ環境を再現しながらシミュレーションを行い、その結果を現実の世界にフィードバックして車両の構成値を調整したり性能を向上させたりする取り組みを実現しています。
他の自動車メーカーの多くが、プロトタイプでデータを収集しながら開発を行っているのに対し、テスラはデジタルツインによりオートパイロットの機能改善や性能向上を図るとともに、ソフトウェアアップデートによる実装の仕組みを既に整えているという意味で、完全自動運転車の開発において先行していると言えるでしょう。
<連載ラインアップ>
■第1回 GAFAM、ウーバー、ネットフリックス、ユニクロが実現するデジタル変革とは?
■第2回 EVの完全受注生産を実現したテスラを貫く「DXの神髄」とは?(本稿)
■第3回 AIと最先端テクノロジーでタクシー市場を変革したウーバーの革新性
■第4回 IoTとAIをフル活用、店舗を急速アップデートするウォルマートのデジタル変革
<著者フォロー機能のご案内>
●無料会員に登録すれば、本記事の下部にある著者プロフィール欄から著者をフォローできます。
●フォローした著者の記事は、マイページから簡単に確認できるようになります。
●会員登録(無料)はこちらから
[もっと知りたい!続けてお読みください →] 「DXで空白の30年を吹っ飛ばそう」OKI CDO坪井氏が信じる日本製造業の力
[関連記事]
5秒で回答、トラスコ中山の“劇的時間短縮”AI見積システムが生まれるまで
経営×AI×現場が融合、日本の製造業を変える「プラスサムゲーム」とは?
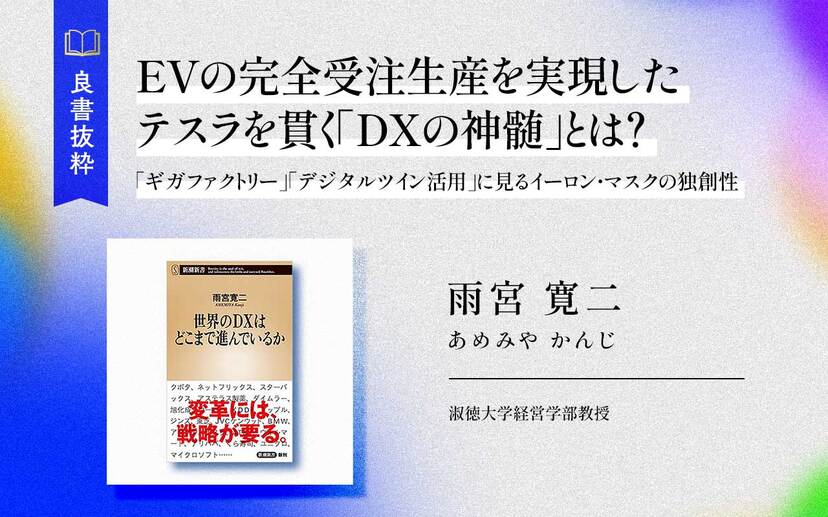
コメント